PVEL’s Backsheet Durability Sequence (BDS) assesses fundamental reliability risks for backsheets including yellowing and cracking. While backsheet cracking is more concerning, yellowing can also be a sign of material degradation that can ultimately allow moisture ingress that causes delamination and/or corrosion.
Backsheet Durability Sequence
Backsheet cracks that allow moisture to enter a PV module can severely impact field performance. Other signs of backsheet aging, such as yellowing and chalking (powder accumulation on the backsheet surface), are potential indications of accelerated degradation. BDS utilizes high temperature and high humidity to stress the backsheet. UV light is applied, which can break polymer chains in backsheets, resulting in degraded mechanical properties and moisture ingress. Cyclic thermal stress allows for the full level of material degradation to be realized.
Test Procedure
The BDS begins with 1,000 hours of damp heat, followed by rear-side UV exposure, then 50 thermal cycles (TC), and finally 10 cycles of humidity freeze (HF). This sequence of UV, TC and HF testing is repeated twice, followed by a short UV exposure for photobleaching, which removes any minor discolorations that only occur in laboratory environments, not in the field. During BDS, PVEL performs visual inspection, electrical insulation resistance testing and colorimeter measurements at ten different backsheet locations for two identical samples per BOM.
These measurements use the Commission Internationale de l’Eclairage (CIE) L*a*b* coordinate system, with b* representing the yellow/blue coordinate. As yellowness increases, so does the b* value. Calculating the delta b* from the average initial measurement throughout the course of BDS quantifies changes in yellowness.
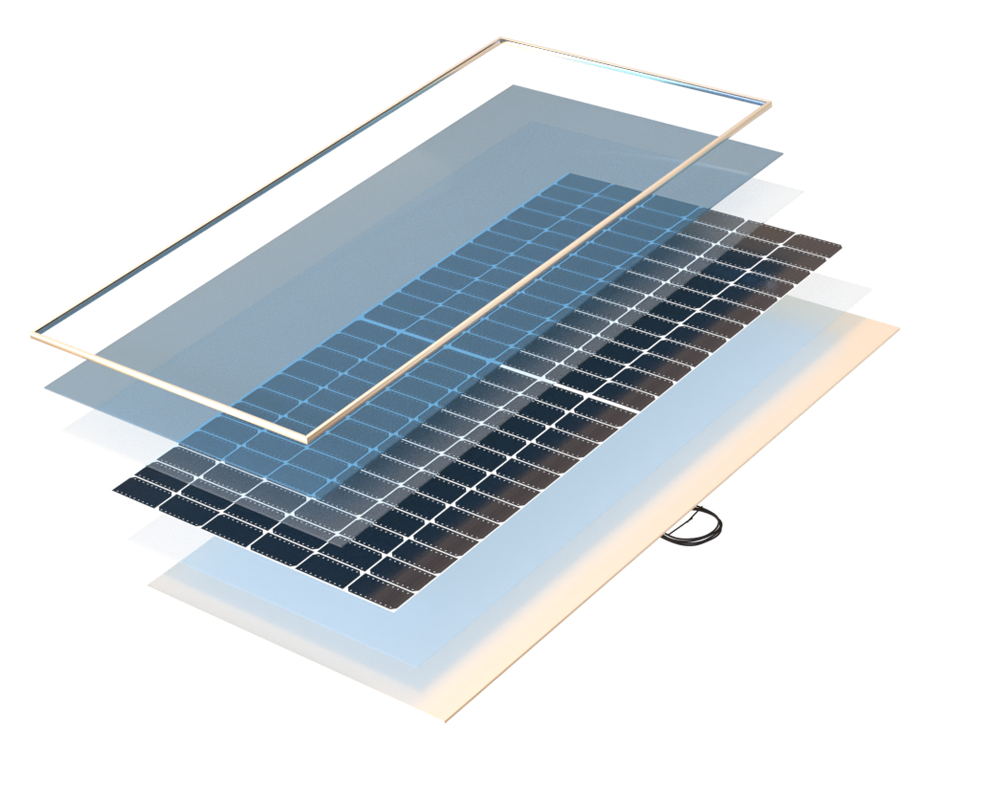
Key Takeaways
Click through the key takeaways below.
Over 10% of BOMs tested had a post-test delta b* value of 8 or more
Since the test was added to the Product Qualification Program in 2019, no PV module tested by PVEL has failed BDS due to backsheet cracking, but over 10% of BOMs tested had a post-test delta b* value of 8 or more, indicating a concerning level of discoloration.
Modules tested may not represent market availability
It is important to note that PVEL has tested about 25% of commercially available backsheets and that high-quality materials are typically used in PQP test samples.
Untested products may present risks
PVEL’s results do not reveal issues with the inferior backsheet products that are certainly being used by some module manufacturers but have not been submitted to PVEL’s PQP testing.
Reading BDS Test Results
Buyers can use the difference between b* values (“delta b star”) at the beginning and end of BDS testing to evaluate backsheet discoloration.
As shown in the graph below, we have observed a broad range of delta b* values, which indicates that some BOMs are made of polymers that are more vulnerable to yellowing than others.
When comparing BOMs with different delta b* values the important factor for buyers to consider is specific project conditions. UV exposure is the primary driver of polymer degradation, so backsheet durability is most important in high irradiance and high albedo conditions.
The backsheet of this fielded PV module is yellowed.
Image source: Bruckman, Laura et. al. Backsheets: Correlation of Long-Term Field Reliability with Accelerated Laboratory Testing. United States. View
Yellowing in BOMs Tested by PVEL
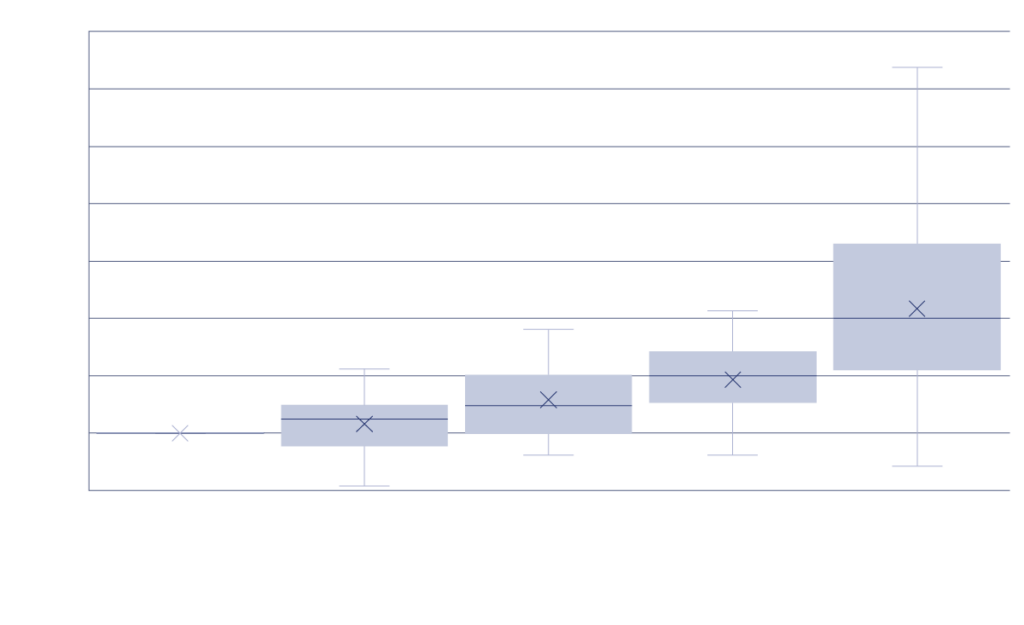
Comparing Glass//Backsheet and Glass//Glass PV Module Designs
Backsheet failure is a widely known problem in solar assets. For example, Schüco, a defunct PV module manufacturer, issued a stark safety warning for asset owners in March 2022: all Schüco PV modules produced from 2010-2012 should be removed and disposed of due to electric shock risks that stem from defective polyamide backsheets.*
Glass//glass PV module designs are one solution to the problem of defective backsheets. While eliminating the potentially problematic backsheet component entirely, they also introduce other reliability risks.
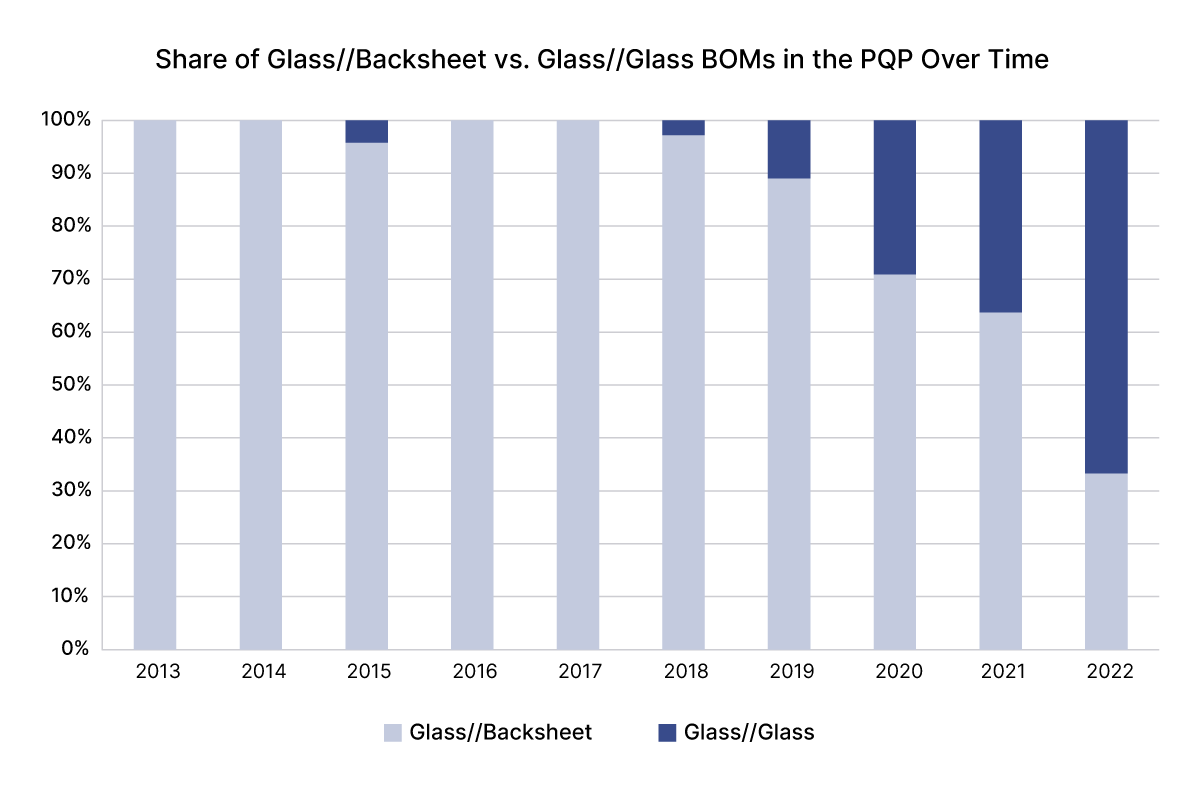
General observations:
- Glass//glass BOMs are more likely to suffer glass breakage during shipment to PVEL and during PVEL’s mechanical stress sequence (MSS) and hail stress sequence (HSS). The glass typically breaks before cell damage occurs.
- Glass//backsheet BOMs are less susceptible to glass breakage, but they are more susceptible to cell damage during shipment and mechanical and hail stress testing.
- PVEL has examples of both glass//glass and glass//backsheet BOMs performing well in damp heat testing. For either design, quality materials and construction are essential to preventing mositure ingress and/or corrosion.
- Glass//glass BOMs marginally outperformed glass//backsheet BOMs in both thermal cycling and PID testing for the 2022 Scorecard with better median and average degradation rates.
Our test results show that glass//glass and glass//backsheet PV module designs can both perform reliably – but only if quality materials are used in their construction.
*Source: Enkhardt, Sandra. “Schüco publishes warning due to potentially defective solar module backsheets”. PV Magazine. 29 March 2022. View
Damp Heat Case Study
PVEL tested two 144 cell BOMs with the same cells and front encapsulants, produced by the same module manufacturer.
- One glass//glass design was a Top Performer in damp heat testing with 1.12% degradation – but a similar glass//backsheet module degraded by 4.95%.
- The glass//glass design had 2.0 mm glass while the glass//backsheet design had 3.2 mm front glass. The BOMs also utilized different cell interconnects, back encapsulants, frames, and frame adhesives.
- The backsheet allowed moisture to enter the laminate leading to cell corrosion. In this scenario, the glass//glass design is clearly more reliable than the glass//backsheet design, yet PVEL has also observed moisture ingress in some glass//glass PV modules.
Reviewing PQP reports and specifying BOMs for procurement is vital for receiving reliable modules.
Go beyond model types. Procure PV modules with top-performing bills of materials.
Join PVEL’s downstream partner network.
Sign Up