PVEL’s Damp Heat (DH) test evaluates the impact of heat and humidity on PV module reliability. We assess susceptibility to moisture ingress, delamination, and corrosion. Projects in hot environments with high humidity require PV modules with top-performing DH results.
Damp Heat
The damp heat test simulates long-term degradation and failure modes that are typical in high temperatures and high humidity conditions. Moisture and heat can weaken the materials binding the PV module together. When the adhesiveness of these materials weakens due to low-quality components and/or substandard lamination processes, moisture can enter the laminate and corrode internal materials. The result is performance loss and safety issues.
Why Testing Matters
Certification testing doesn’t comprehensively assess the risk of delamination in the field. Asset owners may suffer financial losses when PV modules delaminate – even when they’re under warranty.
A recent class-action lawsuit, Ziccarello v. Sanyo Energy (U.S.A.) Corp., awarded damages to some PV asset owners with Sanyo PV modules susceptible to delamination over time. Asset owners waited more than three years for a settlement to be reached.
Only the most severe cases of delamination were eligible for replacement or financial relief. However, the delamination observed in PV modules not eligible for replacement is still likely to result in significant power loss over time and potential safety risks.
Source: Kroll Settlement Administration LLC. “Ziccarello v Sanyo Energy (U.S.A.) Corp.” April 6 2022. View
Asset owners with underperforming, delaminated modules will not be reimbursed for system underperformance – and only the most severely affected asset owners will receive any form of financial relief.
Eligible for Replacement
Delamination was so extreme that the module began to severely corrode.
Not Eligible for Replacement
Without publicly available rationale, the PV module was deemed not eligible for replacement despite indications of significant delamination, including the ingress of dirt and moisture between the glass and the frame.
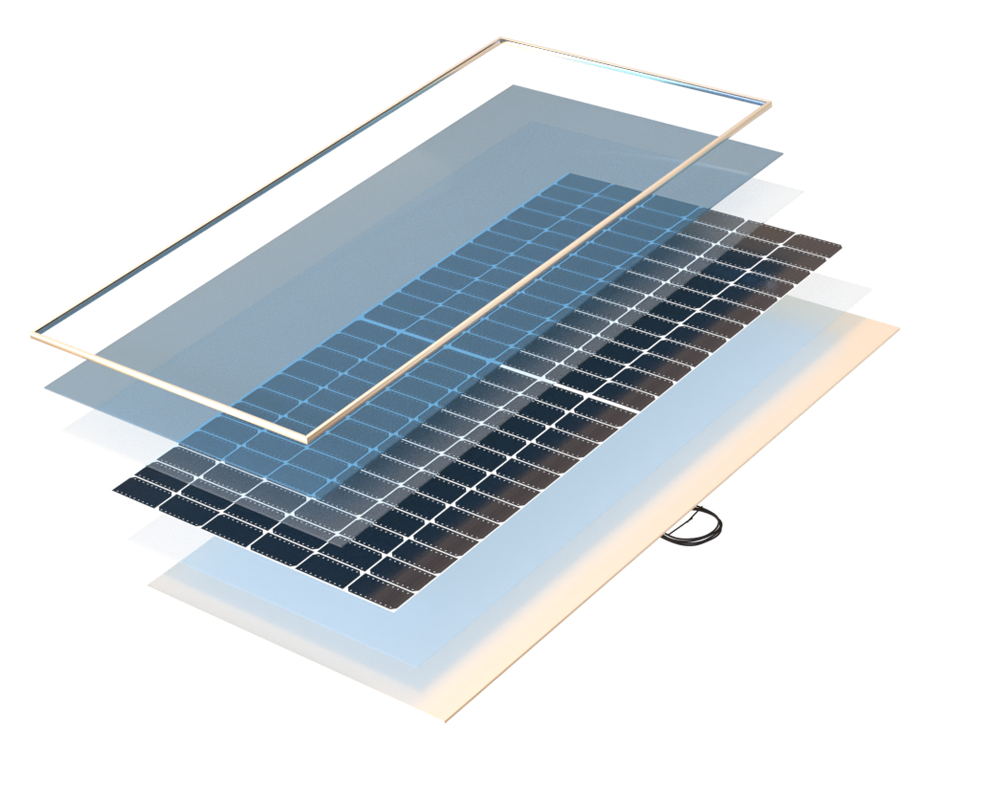
Key Takeaways
Click through the key takeaways below.
50% of BOMs tested for Damp Heat achieved top-performing results
There was a wide range of performance in DH: 50% of BOMs achieved top-performing results after the full test sequence. One BOM degraded by 54%, the worst DH result in PVEL history.
67% decrease in BOMs requiring boron-oxygen stabilization
Only 23% of top-performing BOMs required boron-oxygen stabilization to achieve <2% degradation versus 70% in 2021. This reduction in destabilization makes DH test results much easier for buyers to interpret. These improvements were driven by the increased use of gallium dopants during crystalline cell manufacturing.
Components impact module reliability
Several BOMs with concerning results used near-identical materials to Top Performers from the same manufacturers. This proves that small component changes can severely impact reliability.
Test Procedure
DH subjects modules to a constant 85°C and 85% relative humidity in an environmental chamber for two periods of 1,000 hours. This test doubles the duration required for IEC certification to identify additional module failure modes where the combination of high heat and intense moisture stresses the PV module layers.
Environments with high temperatures and no current can lead to a destabilization of PV cell boron-oxygen (BO) complexes. This leads to power loss in some boron-doped PERC cells, a phenomenon that is not yet well-understood in the field. To reverse this effect PVEL conducts a BO stabilization process at the end of the DH test sequence. This stabilization step helps separate BO-induced power loss from traditional DH-induced power loss.
Power Degradation of Each Model Type
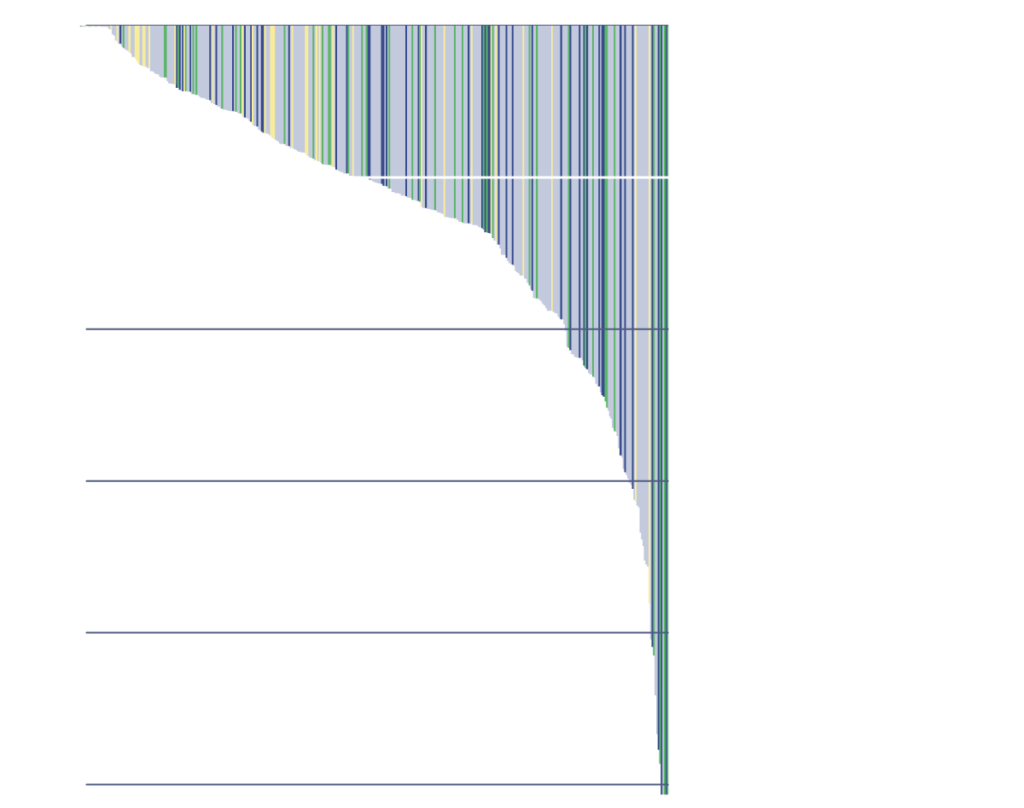
Reading DH Test Results
Modules susceptible to degradation from damp heat suffer from substantial power loss and corrosion, which appear as dark areas around cell perimeters and along cell interconnects in EL images.
Not shown here: a checkerboarding effect is usually apparent in EL images of modules with BO-induced destabilization.
Power Degradation After
1,000 hours: 2.3%
2,000 hours: 12.8%
Deviation from Prestress
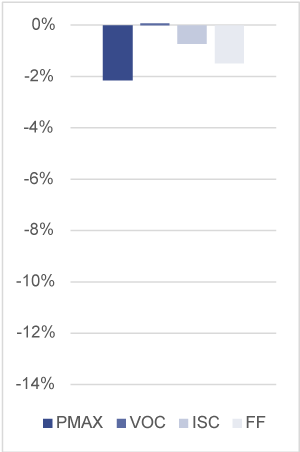
Deviation from Prestress
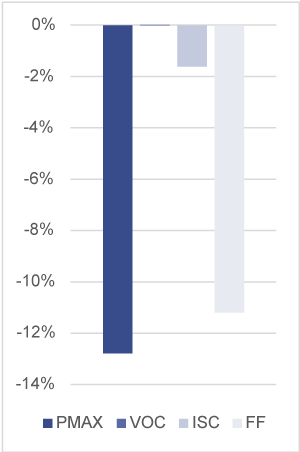
Go beyond model types. Procure PV modules with top-performing bills of materials.
Join PVEL’s downstream partner network.
Sign Up